Using an Electric Torque Wrench or a Tensioner?
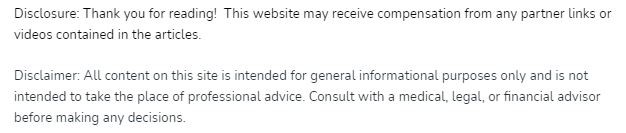

When you have high bolt loads, a bolt tensioner or an electric torque wrench are typically the most common tools for tightening large bolts. In appropriate situations, an electric torque wrench which does not need to connect to a pneumatic hydraulic pump the way a hydraulic tensioner connects, might be the most effective tool. If the bolt load and assembly does require significant loading, then the electric torque wrench may not provide the right tensioning capabilities.
Tensioners come in an assortment of types depending upon application and other related factors. There are variable, fixed, subsea, wind turbine and pump coupling tensioners available for very specific tasks and loads. They can be used, in lieu of an electric torque wrench, in high tensile bolt connections such as on tower crane joints and mast, jib and slew rings bearings.
There are a number of different types of bolt and stud tensioning applications such as with turbines, wind turbines, steam turbines, heat exchangers, pipeline flanges, valve pumps and pressure and reactor vessels. As you get into higher pressure flange connections (perhaps using hydraulic tensioners), it is generally advisable to use a hydraulic flange spreader for medium to high pressure flanges during disassembly and maintenance.
Although tensioners have many applications, there are still situations that can take advantage of an electric torque wrench that operates with a frequency controlled synchronized motor. This type of motor in an electric torque wrench provides a high mounting speed.